Глава 11. Безопасность эксплуатации сосудов и аппаратов, работающих под давлением
11.1. Общие положения
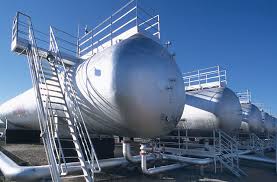
Сосуд — это герметически закрытая емкость, предназначенная для проведения химических, тепловых и других технологических процессов, а также хранения и транспортировки газообразных и жидких веществ. Сосуд ограничен входными и выходными штуцерами.
Основная опасность сосудов работающих под давлением заключается в возможном внезапном разрушении, что сопровождается взрывом, при котором потенциальная энергия сжатой среды в короткий промежуток времени за счет ее адиабатического расширения переходит в кинетическую энергию разлетающихся осколков разрушенного оборудования. Производимая при адиабатическом расширении сжатой среды работа (в Дж) может быть определена по формуле
где p1, p2 - абсолютное давление соответственно в сосуде и в окружающей среде, МПа; V - начальный объем газа, м3; k=cp/cv - показатель адиабаты, для воздуха k=1.41 (здесь сp - удельная теплоемкость газа при постоянном давлении, Дж/(кг×К); сv - то же, при постоянном объеме, Дж/(кг×К)).
Мощность взрыва в МВт
где t - время действия взрыва, с.
Например, при вместимости сосуда 1 м3, находящегося под давлением газа 1 МПа, мощность взрыва составляет более 13 МВт, а водяного пара - около 200 МВт. Взрыв такой мощности сопровождается не только разрушением зданий, но и травматизмом с тяжелым и смертельным исходом.
Основными причинами возникновения аварий и взрывов сосудов, работающих под давлением являются:
- несоответствие конструкции сосуда максимально допустимому давлению и температуре;
- превышение давления сверх предельного;
- потеря механической прочности (при наличии внутренних дефектов металла, коррозии);
- несоблюдение установленного режима работы, недостаточная квалификация обслуживающего персонала и отсутствие технического надзора.
Требования для безопасной эксплуатации таких аппаратов и сосудов изложены в Правилах устройства и безопасной эксплуатации сосудов, работающих под давлением, утвержденных постановлением МЧС Республики Беларусь 27.12.2005 № 56 (далее - Правила по сосудам).
В Правилах по сосудам установлены требования к их проектированию, устройству, изготовлению, реконструкции, наладке, монтажу, ремонту, техническому диагностированию и эксплуатации, которые распространяются:
- на сосуды, работающие под давлением воды с температурой выше 1150С или другой жидкости с температурой, превышающей температуру кипения при давлении 0,07 МПа, без учета гидростатического давления;
- сосуды, работающие под давлением пара или газа свыше 0,07 МПа;
- баллоны, предназначенные для транспортировки и хранения сжатых, сжиженных и растворенных газов под давлением свыше 0,07 МПа;
- сосуды для транспортировки и хранения сжатых и сжиженных газов, давление паров которых при температуре до 500С превышает 0,07 МПа;
- цистерны и сосуды для транспортировки или хранения сжатых и сжиженных газов, жидкостей и сыпучих тел, в которых давление свыше 0,07 МПа создается для их опорожнения;
- барокамеры.
В соответствии с требованиями Правил по сосудам владелец обязан обеспечить содержание сосудов в исправном состоянии и безопасные условия их работы.
В этих целях необходимо:
- назначить приказом из числа специалистов, имеющих высшее или среднее техническое образование, прошедших проверку знаний Правил по сосудам, ответственных по надзору за техническим состоянием и эксплуатацией сосудов и ответственных за исправное состояние и безопасную эксплуатацию сосудов. Повторную проверку знаний указанные специалисты должны проходить один раз в 3 года и не реже одного раза в 5 лет — повышать свою квалификацию;
- назначить необходимое количество лиц обслуживающего персонала, обученного и имеющего удостоверения на право обслуживания сосудов, а также установить такой порядок, чтобы персонал, на который возложены обязанности по обслуживанию сосудов, вел тщательное наблюдение за порученным ему оборудованием путем его осмотра, проверки действия арматуры, контрольно-измерительных приборов, предохранительных и блокировочных устройств и поддержания сосудов в исправном состоянии. Результаты осмотра и проверки должны записываться в сменный журнал;
- обеспечить проведение технических освидетельствований и диагностирования сосудов в установленные сроки;
- обеспечить порядок и периодичность проверки знаний руководителями и специалистами Правил по сосудам;
- организовать периодическую проверку знаний персоналом инструкций по режиму работы, безопасному обслуживанию сосудов, а также вопросам охраны труда;
- обеспечить специалистов Правилами по сосудам и руководящими указаниями по безопасной эксплуатации сосудов, а персонал — инструкциями.
Ответственный по надзору за техническим состоянием и безопасной эксплуатацией сосудов должен осуществлять свою работу по плану, утвержденному руководителем организации. При выявлении неисправностей, а также нарушений Правил по сосудам и инструкций в процессе эксплуатации сосудов, ответственный по надзору за техническим состоянием и эксплуатацией сосудов должен принять меры по устранению этих неисправностей или нарушений, а в случае необходимости принять меры по выводу сосуда из работы. Ответственность за исправное состояние и безопасную эксплуатацию сосудов в организации (цеха, участка) возлагается приказом на работника, которому подчинен персонал, обслуживающий сосуды. Номер и дата приказа о назначении ответственного лица должны быть записаны в паспорте сосуда.
Для управления работой и обеспечения безопасных условий эксплуатации сосуды в зависимости от назначения должны быть оснащены:
- запорной или запорно-регулирующей арматурой;
- приборами для измерения давления;
- приборами для измерения температуры;
- предохранительными устройствами;
- указателями уровня жидкости.
Арматура должна иметь следующую маркировку:
- наименование или товарный знак изготовителя;
- условный проход;
- условное давление, МПа (допускается указывать рабочее давление и допустимую температуру);
- направление потока среды;
- марку материала корпуса.
На маховике запорной арматуры должно быть указано направление его вращения при открывании или закрывании арматуры. Арматура с условным проходом более 20 мм, изготовленная из легированной стали или цветных металлов, должна иметь паспорт установленной формы, в котором должны быть указаны данные по химсоставу, механическим свойствам, режимам термообработки и результатам контроля качества изготовления неразрушающими методами.
Каждый сосуд и самостоятельные полости с разными давлениями должны быть снабжены манометрами прямого действия. Манометр устанавливается на штуцере сосуда или трубопроводе между сосудом и запорной арматурой. Манометры должны иметь класс точности не ниже 2,5— при рабочем давлении сосуда до 2,5 МПа, 1,5— при рабочем давлении сосуда свыше 2,5 МПа. Манометр должен выбираться с такой шкалой, чтобы предел измерения рабочего давления находился во второй трети шкалы. На шкале манометра владельцем сосуда должна быть нанесена красная черта, указывающая рабочее давление в сосуде. Манометр должен быть установлен так, чтобы его показания были отчетливо видны обслуживающему персоналу. Номинальный диаметр корпуса манометров, устанавливаемых на высоте до 2 м от уровня площадки наблюдения за ним, должен быть не менее 100 мм, на высоте от 2 до 3 — не менее 160 мм. Установка манометров на высоте более 3 м от уровня площадки не разрешается.
Между манометром и сосудом должен быть установлен трехходовый кран или заменяющее устройство, позволяющее проводить периодическую проверку манометра с помощью контрольного.
Проверка манометров с их опломбированием и клеймением должна производиться не реже одного раза в 12 месяцев. Кроме того, не реже одного раза в 6 месяцев владельцем сосуда должна производиться дополнительная проверка рабочих манометров контрольными.
Каждый сосуд должен быть снабжен предохранительными устройствами от повышения давления выше допустимого значения.
В качестве предохранительных устройств применяются:
- пружинные предохранительные клапаны;
- рычажно-грузовые предохранительные клапаны;
- импульсные предохранительные устройства, состоящие из главного предохранительного клапана и управляющего импульсного клапана прямого действия;
- предохранительные устройства с разрушающимися мембранами (предохранительные мембраны);
- другие устройства, применение которых согласовано с Госпромнадзором РБ.
Основной характеристикой предохранительных клапанов является их пропускная способность – количество рабочей среды в массовых G, кг/ч, или объемных Q, м3/ч, единицах, сбрасываемое через клапан при установленных значениях давления на входе и выходе (противодавление), конкретных значениях температуры рабочей среды на входе в клапан и определенном ходе золотника.
Пропускную способность предохранительных клапанов и их количество следует выбирать так, чтобы в защищаемой системе не создавалось давление, превышающее избыточное рабочее давление более чем на 0,05 МПа при избыточном рабочем давлении в системе до 0,3 МПа включительно; на 15% - при избыточном рабочем давлении до 6МПа включительно и на 10% - при избыточном рабочем давлении свыше 10 МПа. Для газов и паров она рассчитывается по формуле
G = 216 Ра Ö М/Т,
где Р – давление под клапаном, Па (максимальное давление под клапаном должно быть не более 1,1 расчетного); а – площадь сечения клапана, см2; М – молекулярная масса газов или паров (для воздуха М = 29 кг/кмоль, для водяного пара – 18 кг/кмоль); Т – абсолютное значение температуры пара или воды в котле, К.
Количество предохранительных клапанов рассчитывают по формуле
n = kGk / pdh,
где к – коэффициент, для малоподъмных клапанов равный 0,0075, для полноподъемных – 0,015; Gk- - производительность котла по пару при максимальной нагрузке, кг/ч; p – абсолютное давление пара в котле, Па; d – внутренний диаметр тарелки клапана, см; h – высота подъема клапана, см.
Значение отношения высоты подъема клапана к внутреннему диаметру тарелки определяет его тип:
Н = h/d
При Н £ 0,05 клапан считают малоподъемным, при 0,05 £ Н £ 0,25 - полноподъемным.
Распространенным средством защиты технологического оборудования от разрушения при взрывах являются предохранительные мембраны (разрывные, ломающиеся, срезные, хлопающие, специальные) и взрывные клапаны (рис. 11.1, 11.2).
Достоинством предохранительных мембран является предельная простота их конструкции, что характеризует их как самые надежные из всех существующих средств взрывозащиты. Кроме того, мембраны практически не имеют ограничений по пропускной способности. Существенным недостатком предохранительных мембран является то, что после срабатывания защищаемое оборудование остается открытым, это, как правило, приводит к остановке технологического процесса и к выбросу в атмосферу всего содержимого аппарата. При разгерметизации технологического оборудования нельзя исключить возможность вторичных взрывов, которые обусловлены подсосом атмосферного воздуха внутрь аппарата через открытое отверстие мембраны.
Разрывные мембраны изготавливают из тонколистовых материалов с учетом свойств и температуры рабочих сред (алюминий, медь, никель, титан и его сплавы, свинец, различная сталь).
Толщину мембраны S ориентировочно можно определить по формуле
S = Рразр х Dу/(Кр х sпч),
где Рразр - разрушающее давление, Па; Dу – условный проход мембраны, мм; Кр – коэффициент, принимаемый в пределах от 3,3 до 4,2; sпч – предел прочности тонколистового материала МПа. Рразр можно определить из выражения
К = Рразр / Рраб,
где К принимается в пределах от 1,2 до 1,3; Рраб – рабочее давление в аппарате.
Предохранительные мембраны должны быть маркированы, где указывается наименование или товарный знак изготовителя, номер партии мембран, тип, условный и рабочий диаметры, материал, минимальное и максимальное давление срабатывания при заданной температуре и при 200С.
Использование на технологическом оборудовании взрывных клапанов дает возможность устранить эти негативные последствия, так как после срабатывания и сброса отверстие вновь закрывается и таким образом не вызывает необходимости немедленной остановки оборудования и проведения восстановительных работ. К недостаткам взрывных клапанов следует отнести их большую инерционность по сравнению с мембранами, сложность конструкции, а также недостаточную герметичность, ограничивающую область их применения (они могут использоваться для взрывозащиты оборудования, работающего при нормальном давлении).
Наиболее распространенным средством защиты технологического оборудования от взрыва являются предохранительные клапаны. Однако и они имеют ряд существенных недостатков, в основном определяющихся большой инерционностью подвижных деталей клапанов.
Порядок и сроки проверки исправности действия предохранительных устройств в зависимости от условий технологического процесса должны быть указаны в инструкции по эксплуатации предохранительных устройств.
11.2. Требования безопасности при проектировании, эксплуатации
и установке стационарных сосудов, работающих под давлением
Проектирование сосудов и их элементов, а также выполнение проекта их монтажа или реконструкции осуществляются специализированными организациями. Проекты, технические условия и возможные изменения в проекте и нормативных документах на изготовление сосудов согласуются и утверждаются в установленном Госпромнадзором порядке.
Конструкция сосудов должна обеспечивать надежность и безопасность их эксплуатации в течение расчетного срока службы и предусматривать возможность проведения технического освидетельствования, очистки, промывки, полного опорожнения, продувки, ремонта и эксплуатационного контроля металла и соединений.
Устройства, препятствующие наружному и внутреннему осмотру сосудов (мешалки, змеевики, рубашки, тарелки, перегородки и другие приспособления), должны быть съемными. Сосуды должны иметь штуцеры для наполнения и слива воды, а также удаления воздуха при гидравлическом испытании. На каждом сосуде предусматривается установка вентиля, крана или другого устройства, позволяющего осуществлять контроль за отсутствием давления в сосуде перед его открыванием; при этом отвод среды должен быть направлен в безопасное место.
В конструкции сосудов, обогреваемых горячими газами, должно быть предусмотрено надежное охлаждение стенок до расчетной температуры.
Сосуды снабжаются необходимым количеством люков и смотровых лючков, позволяющих производить их осмотр, очистку и ремонт, а также монтаж и демонтаж разборных внутренних устройств.
Сосуды с внутренним диаметром более 800 мм имеют люки, а с внутренним диаметром 800 мм и менее - лючки. Люки и лючки располагают в местах, доступных для обслуживания. Крышки люков должны быть съемными.
Сосуды могут иметь следующие днища: эллиптические, полусферические, торосферические, конические, плоские и др.
Сварные швы в сосудах выполняют в стык. Они должны быть доступны для контроля при изготовлении, монтаже и эксплуатации сосудов. Отверстия для люков, лючков и штуцеров располагают вне сварных швов.
Материалы, применяемые для изготовления сосудов, должны обеспечивать их надежную работу в течение расчетного срока службы с учетом заданных условий эксплуатации (расчетное давление, минимальная отрицательная и максимальная расчетная температура), состава и характера среды (коррозионная активность, взрывоопасность, токсичность и др.) и влияния температуры окружающего воздуха. Для изготовления, монтажа и ремонта сосудов и их элементов применяют основные материалы, качество и свойства которых соответствуют установленным стандартам и техническим условиям.
Изготовление, реконструкцию, монтаж, наладку и ремонт сосудов и их элементов выполняют специализированные организации, располагающие техническими средствами, необходимыми для качественного выполнения работ в соответствии с технологией, разработанной до начала работ организацией, их осуществляющей.
Сварные соединения подвергают контролю различными способами, которые гарантируют их высокое качество и надежность эксплуатации, а также позволяют выявлять дефекты.
Приемочный контроль изделия, сборочных единиц и сварных соединений производят после окончания всех технологических операций, связанных с термической обработкой, деформированием и наклепом металла. Результаты по каждому виду контроля фиксируются в отчетной документации (журналах, формулярах, протоколах, маршрутных паспортах и т.д.).
Гидравлическому (пневматическому) испытанию сосудов подлежат все сосуды, готовые к эксплуатации. Сосуды, изготовление которых заканчивается на месте установки и транспортируемые для монтажа частями, подвергаются гидравлическому испытанию прямо на месте монтажа. Сосуды, имеющие защитное покрытие (изоляцию) или наружный кожух, подвергаются гидравлическому испытанию до наложения покрытия (изоляции) или до установки кожуха.
Сосуды устанавливают на открытых площадках в местах, исключающих скопление людей, или в отдельно стоящих зданиях.
Допускается установка сосудов в помещениях, примыкающих к производственным зданиям, при условии отделения их от здания капитальной стеной, в производственных помещениях, с заглублением в грунт при условии обеспечения доступа обслуживающего персонала к арматуре и защиты стенок сосуда от коррозии. Не разрешается установка сосудов в жилых, общественных и бытовых зданиях, а также в примыкающих к ним помещениях.
Сосуды следует размещать с учетом обеспечения возможности их осмотра, ремонта и очистки с внутренней и наружной стороны и исключения их опрокидывания. Для удобства обслуживания сосудов их оборудуют площадками и лестницами.
Техническое освидетельствование сосудов. После монтажа до пуска в работу сосуды подвергают техническому освидетельствованию. Периодически в процессе эксплуатации проводят и внеочередное освидетельствование, которое осуществляют специалисты организации, имеющей лицензию на проведение экспертизы промышленной безопасности технических устройств (сосудов).
Сосуды, предназначенные для работы со средой, вызывающей разрушение и физико-химическое превращение материала (например, коррозию), подвергают наружному и внутреннему осмотру один раз в 4 года, гидравлическому испытанию — один раз в 8 лет.
При первичном освидетельствовании это позволяет удостовериться в том, что сосуд установлен и оборудован в соответствии с Правилами и не имеет повреждений. При периодических и внеочередных освидетельствованиях подтверждают исправность сосуда и возможность его дальнейшей эксплуатации.
С целью проверки прочности элементов сосуда и плотности его соединений проводят гидравлическое испытание, которому подвергают сосуд вместе с установленной на нем арматурой.
Перед внутренним осмотром и гидравлическим испытанием сосуд должен быть остановлен, охлажден (отогрет), освобожден от заполняющей его рабочей среды, отключен заглушками от всех трубопроводов, соединяющих сосуд с источником давления или с другими сосудами. Металлические сосуды должны быть очищены до металла. Сосуды, предназначенные для работы с вредными веществами 1-го и 2-го классов опасности, подвергают тщательной обработке (нейтрализации, дегазации). Должны быть отключены электрообогрев и привод сосуда.
Внеочередное освидетельствование сосудов, находящихся в эксплуатации, проводят в следующих случаях: если сосуд не эксплуатировался более 12 месяцев; если он был демонтирован и установлен на новом месте; если произведено выправление выпучин, или вмятин, а также реконструкция или ремонт сосуда с применением сварки или пайки элементов, работающих под давлением; перед наложением защитного покрытия на стенки сосуда; после аварии сосуда или элементов, работающих под давлением; по требованию ответственного лица по надзору за техническим состоянием и эксплуатацией сосуда. При проведении внеочередного освидетельствования указывают причину, по которой было проведено освидетельствование.
Техническое освидетельствование сосудов производят на специальных ремонтно-испытательных пунктах, в организациях - изготовителях, на наполнительных станциях, а также в организациях-владельцах, располагающих необходимой базой и оборудованием для этого. Результаты технического освидетельствования записывают в паспорте сосуда с указанием разрешенных параметров эксплуатации сосуда и сроков следующих освидетельствовали.
Если при освидетельствовании были проведены дополнительные испытания, в паспорте записывают виды и результаты этих испытаний, а также причины, вызвавшие их необходимость.
Если при освидетельствовании обнаруживают дефекты, снижающие прочность сосуда, то его дальнейшая эксплуатация разрешается при пониженных параметрах (давлении и температуре), что должно быть подтверждено расчетом на прочность. Это решение записывают в паспорте.
Сосуд не допускается к дальнейшей эксплуатации, если при техническом освидетельствовании было выявлено, что он вследствие имеющихся дефектов или нарушений не соответствует требованиям существующих Правил. Сосуды, предназначенные для вредных веществ (жидкостей и газов) 1-го и 2-го классов опасности, подвергаются испытанию на герметичность воздухом или инертным газом при давлении, равном рабочему. При наружном и внутреннем осмотрах должны быть выявлены все дефекты, снижающие прочность сосудов. При этом особое внимание обращают на выявление таких дефектов на поверхностях сосуда, как трещины, надрывы, коррозия стенок (особенно в местах отбортовки и вырезок), выпучины, отдушины (преимущественно у сосудов с «рубашками», а также на сосудах с огневым или электрическим обогревом), раковины (в литых сосудах); дефекты сварки, надрывы, разъедания (в сварных швах); трещины между заклепками, обрывы головок, следы пропусков, надрывы в кромках склепанных листов, коррозионные повреждения заклепочных швов, зазоры под кромками клепаных листов и головками заклепок (в заклепочных швах); разрушения футеровки, в том числе неплотности слоев футеровочных плиток, трещины в гуммированном, свинцовом или ином покрытии, сколы эмали, трещины и отдулины в плакирующем слое, повреждения металла стенок сосуда в местах наружного защитного покрытия (в сосудах с защищенными от коррозии поверхностями).
Гидравлическое испытание сосудов проводят только при удовлетворительных результатах наружного и внутреннего осмотров.
Сосуды до пуска в эксплуатацию регистрируют в соответствии с Инструкцией о регистрации объектов в государственном реестре опасных производственных объектов и ведении государственного реестра опасных производственных объектов, утвержденной Постановлением МЧС РБ 11.04. 2003 г. № 22.
После регистрации сосуда на основании результатов технического освидетельствования и проверки инспектор выдает разрешение на ввод в его эксплуатацию. Этот документ должен быть отмечен в паспорте сосуда. На каждом сосуде после выдачи разрешения на его эксплуатацию краской на видном месте или на специальной табличке должны быть указаны регистрационный номер, разрешенное давление, дата очередного наружного и внутреннего осмотра и проведения гидравлического испытания.
Сосуд должен быть выведен из эксплуатации в случаях: превышения давления в сосуде выше разрешенного; выявления неисправности предохранительных устройств; обнаружения в элементах сосуда неплотностей, выпучин, разрывов прокладок; неисправности манометра и невозможности определения давления иными способами; падения уровня жидкости в сосудах с огневым обогревом ниже допустимого; выхода из строя указателей уровня жидкости; неисправности предохранительных блокировочных устройств; возникновения пожара, угрожающего сосуду.
Порядок аварийной остановки сосуда и последующего ввода его в работу указывается в инструкции.
11.3. Безопасность эксплуатации баллонов с сжатыми, сжиженными и растворенными газами
Баллон - это сосуд, предназначенный для транспортировки, хранения и использования сжатых (кислород, водород, азот и воздух), сжиженных (хлор, аммиак, пропан, сероводород и диоксид углерода) или растворенных (ацетилен) под давлением газов.
При эксплуатации баллонов могут происходить взрывы, причинами которых являются:
- повреждение корпуса баллона в случае его падения или удара до нему (особенно при температуре ниже -30°С, когда повышается хрупкость стали, из которой изготовлен баллон);
- повышение температуры газа в баллоне, приводящее к росту давления и разрыву баллона;
- переполнение баллона сжиженными газами, приводящее к возрастанию давления выше допустимого (для предотвращения этого 10 % объема баллона оставляют свободными);
- попадание масла и других жировых веществ во внутреннюю полость вентилей кислородных баллонов (для предотвращения этого вентили кислородных баллонов ввертывают на глете, фольге или с применением жидкого натриевого стекла);
- загрязнение водорода (в случае водородных баллонов) кислородом в количестве более 1 % по объему, например при кислородно-водородной сварке, водородной коррозии, при накоплении в баллонах окалины.
Баллоны, в которых давление сжатых газов достигает 15 МПа, изготавливают главным образом из цельнотянутых бесшовных стальных труб. Для хранения газов под давлением до 3 МПа допускается применение сварных баллонов.
Баллоны оснащают вентилями, плотно ввернутыми в отверстия горловины. Боковые штуцеры вентилей баллонов, наполняемые водородом и горючими газами, имеют левую резьбу, а баллоны, наполняемые кислородом и негорючими газами, - правую резьбу. Вентили баллонов для взрывоопасных горючих веществ, а также вредных веществ 1-го и 2-го классов опасности снабжаются заглушкой. На баллонах вместимостью более 100 л устанавливают предохранительные клапаны. Для устойчивости в вертикальном положении на нижнюю сферическую часть баллона насаживают стальной башмак.
На верхней сферической части каждого баллона клеймением наносят следующие данные: товарный знак изготовителя; номер баллона; фактическая масса порожнего баллона (кг); дата изготовления и год очередного освидетельствования; рабочее давление, МПа (кгс/см2); пробное гидравлическое давление, МПа (кгс/см2); вместимость баллонов (л); клеймо ОТК изготовителя;
Наружную поверхность баллонов окрашивают в соответствующий цвет (табл. 11.1).
Окраску баллонов и нанесение надписей на них производят масляными, эмалевыми или нитрокрасками. Надписи на баллонах наносят по окружности на длину не менее 1/3 окружности, а полосы — по всей окружности.
Баллоны, находящиеся в эксплуатации, подвергают периодическому освидетельствованию.
Баллоны, установленные стационарно, а также находящиеся постоянно на передвижных средствах, в которых хранят сжатый воздух, кислород, азот, аргон, гелий и обезвоженную углекислоту, экспертом органа технадзора подвергаются наружному и внутреннему осмотру и гидравлическому испытанию под пробным давлением один раз в 10 лет. Все остальные баллоны, а также баллоны со средой, вызывающей разрушение и физико-химическое превращение материалов (коррозию и т.п.), подвергаются наружному и внутреннему осмотру один раз в 4 года и гидравлическому испытанию пробным давлением один раз в 8 лет.
Освидетельствование баллонов осуществляют в отдельных, специально оборудованных помещениях. Температура воздуха в этих помещениях должна быть не ниже 120С. Для внутреннего осмотра баллонов допускается применение электрического освещения с напряжением не выше 12В. Освидетельствование баллонов включает: осмотр внутренней и наружной поверхности баллона; проверку массы и вместимости; проведение гидравлического испытания.
Осмотр баллонов осуществляется для выявления на стенках следов коррозии, трещин, плен, вмятин и других повреждений с целью установления их пригодности для дальнейшей эксплуатации. Перед осмотром баллоны тщательно очищают и промывают водой, а в необходимых случаях проводят промывку специальным растворителем или дегазирование.
Баллоны, на наружной и внутренней поверхности которых при осмотре были выявлены трещины, плены, вмятины, отдулины, раковины и риски глубиной более 10% от номинальной толщины стенки, надрывы и выщербления, износ резьбы горловины, а также те, для которых отсутствуют какие-то паспортные данные, выбраковывают.
Проверяют массу и емкость баллонов. Бесшовные стандартные баллоны вместимостью от 12 до 55 л при уменьшении массы на 7,5 % и более, а также при увеличении их вместимости более чем на 1 % бракуют и изымают из эксплуатации. Емкость баллона определяют как разность между массой баллона, наполненного водой, и массой опорожненного баллона или используют для этого мерные бачки.
Таблица 11.1. Окраска и нанесение надписей на баллоны
Наименование |
Окраска баллонов |
Текст надписи |
Цвет надписи |
Цвет полосы |
Азот |
Черная |
Азот |
Желтый |
Коричневый |
Аммиак |
Желтая |
Аммиак |
Черный |
- |
Аргон сырой |
Черная |
Аргон сырой |
Белый |
Белый |
Аргон |
Черная |
Аргон |
Синий |
Синий |
Аргон чистый |
Серая |
Аргон чистый |
Зеленый |
Зеленый |
Ацетилен |
Белая |
Ацетилен |
Красный |
- |
Бутилен |
Красная |
Бутилен |
Желтый |
Черный |
Нефтегаз |
Серая |
Нефтегаз |
Красный |
- |
Бутан |
Красная |
Бутан |
Белый |
- |
Водород |
Темно-зеленая |
Водород |
Красный |
- |
Воздух |
Черная |
Сжатый воздух |
Белый |
- |
Гелий |
Коричневая |
Гелий |
Белый |
- |
Закись азота |
Серая |
Закись азота |
Черный |
- |
Кислород |
Голубая |
Кислород |
Черный |
- |
Кислород |
Голубая |
Кислород |
Черный |
- |
Сероводород |
Белая |
Сероводород |
Красный |
Красный |
Сернистый |
Черная |
Сернистый |
Белый |
Желтый |
Углекислота |
Черная |
Углекислота |
Желтый |
- |
Фосген |
Защитная |
- |
- |
Красный |
Фреон-11 |
Алюминиевая |
Фреон-11 |
Черный |
Синий |
Фреон-12 |
Алюминиевая |
Фреон-12 |
Черный |
- |
Фреон-13 |
Алюминиевая |
Фреон-13 |
Черный |
2 красные |
Фреон-22 |
Алюминиевая |
Фреон-22 |
Черный |
2 желтые |
Хлор |
Защитная |
- |
- |
Зеленый |
Циклопропан |
Оранжевая |
Циклопропан |
Черный |
- |
Этилен |
Фиолетовая |
Этилен |
Красный |
- |
Все другие |
Красная |
Наименование газа |
Белый |
- |
Все другие |
Черная |
Наименование газа |
Желтый |
- |
Забракованные баллоны независимо от их назначения должны быть приведены в негодное состояние, например, путем нанесения насечек на резьбу горловины или просверливания отверстий на корпусе, что исключает возможность их дальнейшего использования.
Баллоны, прошедшие осмотр, проверку массы и емкости, подвергают гидравлическому испытанию пробным давлением воды, в 1,5 раза превышающем рабочее давление в течение 1 мин. После проведения гидравлического испытания баллоны подвергают пневматическому испытанию давлением воздуха или инертных газов, равном рабочему. Во время пневматического испытания баллоны должны быть погружены в ванну с водой на глубину 1 м.
Баллоны, переведенные на эксплуатацию при пониженном давлении, можно использовать для заполнения газами, рабочее давление которых не превышает допустимое. При этом на них указывают массу, рабочее давление, пробное давление и дату проведенного и следующего освидетельствования, а также клеймо испытательного пункта.
Наполненные газом баллоны, рассчитанные на длительный период складского хранения, подвергают освидетельствованию в выборочном порядке в количестве не менее 5 штук от партии из 100 баллонов, 10 штук от партии до 500 баллонов и 20 штук от: партии, включающей свыше 500 баллонов.
При удовлетворительных результатах освидетельствования срок хранения баллонов продлевают, но не более чем на 2 года.
При неудовлетворительных результатах освидетельствования производят повторное освидетельствование баллонов в таком же количестве. Если и при повторном освидетельствовании результаты оказались неудовлетворительными, дальнейшее хранение всей партии баллонов не допускается. Газ из баллонов удаляют, после чего их подвергают техническому освидетельствованию каждый в отдельности.
При эксплуатации баллонов находящийся в них газ запрещается расходовать полностью. Остаточное давление газа в баллоне должно быть не менее 0,05 МПа (0,5 кгс/см2).
Выпуск газов из баллонов в емкости с меньшим рабочим давлением осуществляется через редуктор, предназначенный именно для данного газа и окрашенный в соответствующий цвет (рис. 11.3).
Баллоны с газами могут храниться как в специальных помещениях, так и на открытом воздухе, в последнем случае они должны быть защищены от атмосферных осадков и солнечных лучей.
Складское хранение в одном помещении баллонов с кислородом и горючими газами запрещается.
Баллоны с газом, устанавливаемые в помещениях, должны находиться на расстоянии не менее 1 м от радиаторов отоплений других отопительных приборов и печей и не менее 5 м — от источников тепла с открытым огнем.
Для безопасного наполнения баллона с целью исключения его переполнения на камере низкого давления редуктора устанавливают манометр и пружинный предохранительный клапан, отрегулированный на соответствующее разрешенное давление в емкости, в которую перепускается газ.
Запрещается наполнять газом баллоны, у которых истек срок назначенного освидетельствования или срок проверки пористой массы, поврежден корпус баллона, не исправны вентили, отсутствуют надлежащая окраска или надписи, не указано избыточное давление газа и нет клеймения.
Наполненные баллоны с насаженными на них башмаками хранят в вертикальном положении. Для предохранения от падения их устанавливают в специально оборудованные гнезда или ограждают барьером.
Баллоны без башмаков можно хранить в горизонтальном положении на деревянных рамах или стеллажах. При хранении на открытых площадках разрешается укладывать баллоны с башмаками в штабели с прокладками из веревки, деревянных брусьев или резины между горизонтальными рядами. При этом высота штабеля не должна превышать 1,5 м. Вентили баллонов должны быть обращены в одну сторону.
Хранят баллоны в одноэтажных складских помещениях с перекрытиями легкого типа без чердаков, окна и двери которых открываются наружу. Стены, перегородки и покрытия складов выполняют из несгораемых материалов не ниже II степени огнестойкости. Для окон и дверей используют матовые или закрашенные белой краской стекла. Высота складских помещений должна быть не менее 3,25 м.
Полы складов должны быть ровные с нескользкой поверхностью, а складов для баллонов с горючими газами - с поверхностью из материалов, исключающих искрообразование при ударе.
В складах вывешивают инструкции, плакаты по правилам обращения с баллонами. Склады оборудуют естественной или искусственной вентиляцией в соответствии с требованиями санитарных норм при проектировании. Склады с баллонами, в которых содержатся взрыво- и пожароопасные газы, располагают в зоне молниезащиты.
Складское помещение для хранения баллонов разделяют несгораемыми стенами на отсеки, в каждом из которых допускается хранение не более 500 баллонов (40 л) с горючими или ядовитыми газами и не более 1 000 баллонов (40 л) с негорючими и неядовитыми газами. В отсеках предусматривается наличие открытых проемов для прохода людей и транспортировки средств механизации. Каждый отсек имеет самостоятельный выход наружу.
Со складов потребителям баллоны транспортируют на специальных тележках или носилках. Ручная переноска баллонов строго запрещена. Перевозка наполненных газами баллонов производится на рессорном транспорте или автокарах в горизонтальном положении обязательно с прокладками между баллонами. В качестве прокладок применяют деревянные бруски с вырезанными гнездами для баллонов, а также веревочные или резиновые кольца толщиной не менее 25 мм (по два кольца на баллон) или другие прокладки, предохраняющие баллоны от ударов друг о друга. Все баллоны во время перевозки укладывают вентилями, направленными в одну сторону.
Для перевозки баллонов в вертикальном положении используют специальные контейнеры, можно перевозить и без них, но обязательно с прокладками между баллонами и ограждением во избежание возможного падения.
Транспортировку и хранение баллонов производят с навернутыми колпаками.
Конструкция баллонов для растворенного ацетилена в целях безопасной эксплуатации предусматривает их заполнение пористой массой и растворителем. В качестве пористой массы используют активированный уголь, в качестве растворителя — ацетон. После заполнения баллонов пористой массой и растворителем на его горловине выбивают массу тары (масса баллона с пористой массой и растворителем, башмаком, кольцом и вентилем).
Баллоны для ацетилена подвергают пневматическому испытанию в организациях, осуществляющих их наполнение пористой массой.
Освидетельствование баллонов для ацетилена производят на ацетиленовых наполнительных станциях не реже чем через 5 лет. Оно включает в себя осмотр наружной поверхности, проверку состояния пористой массы и проведение пневматического испытания.
Состояние пористой массы в баллонах с ацетиленом проверяют на наполнительных станциях не реже чем один раз в 24 мес. При удовлетворительном состоянии пористой массы на каждом баллоне указывают год и месяц проверки, клеймо наполнительной станции, клеймо с изображением букв «Пм», удостоверяющее проверку на соответствие требованиям к пористой массе.
Баллоны для ацетилена с пористой массой при освидетельствовании испытывают азотом под давлением 3,5 МПа (35 кгс/см2). При этом баллоны погружают в воду на глубину 1 м. Чистота азота должна быть не ниже 97 %.
11.4. Цистерны и бочки для перевозки сжиженных газов
Цистерны и бочки также относятся к передвижным сосудам, работающим под давлением, однако специфика их эксплуатации определяет ряд дополнительных требований, которые оговорены в Правилах по сосуда
Цистерна — это передвижной сосуд, постоянно установленный на раме железнодорожного вагона, на шасси автомобиля (прицепа) или на других средствах передвижения и предназначенный для транспортировки и хранения газообразных, жидких и сыпучих веществ.
Бочка — это сосуд цилиндрической или другой формы, который можно перекатывать с одного места на другое и ставить на торцы без дополнительных опор. Бочки предназначены для транспортировки и хранения жидких и других веществ.
Цистерны и бочки для сжиженных газов, за исключением криогенных жидкостей, рассчитывают на давление, которое может возникнуть в них при температуре 500С, автоцистерны — на давление, соответствующее метеорологическим условиям местности, где они будут эксплуатироваться, но не ниже 350С.
Цистерны для сжиженного кислорода и других криогенных жидкостей рассчитывают на давление, при котором будет производиться их опорожнение.
Железнодорожная цистерна в верхней части имеют люк диаметром не менее 450 мм и при необходимости помост около люка с металлическими лестницами по обе стороны цистерны, снабженными поручнями. Автоцистерны оснащены круглыми люками диаметром не менее 450 мм или люками овальной формы соответствующих размеров.
Для предупреждения перегрева цистерны делают термоизолированными или с теневой защитой. Термоизоляционный кожух цистерн для кислорода и других криогенных жидкостей снабжен разрывной мембраной.
В паспортах на цистерны и бочки указывают: наименование изготовителя; номер цистерны (бочки); год изготовления и дата освидетельствования; вместимость цистерн (м3) и бочек (л); массу цистерны в порожнем состоянии без ходовой части (т) и массу бочки (кг); величину рабочего и пробного давления; клеймо ОТК изготовителя; дату проведенного и очередного освидетельствования.
На цистернах клеймо наносят по окружности фланца для люка, а на бочках — на днищах, где располагается арматура. Места клеймения на цистернах и бочках, предназначенных для перевозки сжиженных газов, вызывающих коррозию, после нанесения паспортных данных покрывают антикоррозионным бесцветным лаком.
Окраска новых цистерн и бочек, а также нанесение на них полос и надписей осуществляется изготовителем, а цистерн и бочек, находящихся в эксплуатации, — организацией, производящей их наполнение. Окраску, нанесение полос и надписей на железнодорожные пропан-бутановые и пентановые цистерны, находящиеся в эксплуатации, выполняет владелец цистерн.
Цистерны оснащают вентилями с сифонными трубками для слива и налива среды, вентилем для выпуска паров из верхней части цистерны, пружинным предохранительным клапаном, штуцером для подсоединения манометра, указателем уровня жидкости.
Установленный на цистерне предохранительный клапан оборудуют колпаком с отверстиями для выпуска газа в случае открытия клапана (рис. 11.4).
Каждый наливной и спускной вентиль должен быть снабжен заглушкой.
На днище бочек (кроме бочек для хлора и фосгена) установлен вентиль для наполнения и слива среды. У бочек для хлора и фосгена наливной и сливной вентили снабжены сифонами.
Цистерны и бочки можно заполнять только тем газом, для перевозки и хранения которого они предназначены.
Наружную поверхность цистерн и бочек окрашивают эмалью или алюминиевой краской в светло-серый цвет и наносят на нее предупредительные надписи и отличительные полосы. Отличительные полосы наносят по всей длине корпуса цистерны по средней линии, а надписи — с каждой стороны корпуса над полосой, с левой стороны — наименование газа, с правой — остальные надписи (рис. 11.5). На бочки наносят две отличительные полосы по окружности на расстоянии 200 мм от каждого днища, а надписи делают между полосами. Все цистерны и бочки, зарегистрированные в органе технадзора и находящиеся в эксплуатации, проходят техническое освидетельствование (наружный осмотр и гидравлическое испытание), периодичность которого составляет: для железнодорожных цистерн, предназначенных для транспортировки предельных углеводородов (пропан-бутана и пентана) и изолированных на основе вакуума - 10 лет, для цистерн, предназначенных для перевозки аммиака - через 8 лет, для всех остальных цистерн, включая цистерны для сжиженных газов, вызывающих разрушение и физико-химическое превращение материала (коррозию и т.п.) со скоростью более 0,1 мм/год - наружный и внутренний осмотры - 4 года, гидравлическое испытание - 8 лет.
Перед наполнением цистерн и бочек газами проводят тщательный осмотр наружной поверхности, проверяют исправность и герметичность арматуры, наличие остаточного давления и соответствие параметров имеющегося в них газа назначению цистерны или бочки.
Запрещается наполнять газом неисправные цистерны или бочки, если не исправны арматура и контрольно-измерительные приборы, отсутствует надлежащая окраска или надписи, в цистернах или бочках находится не тот газ, для которого они предназначены, а также истек срок их освидетельствования.
После наполнения цистерн или бочек газом на боковые штуцеры вентилей устанавливают заглушки, а арматуру цистерн закрывают предохранительным колпаком, который затем пломбируют.
11.5. Меры безопасности при эксплуатации газового хозяйства
На многих предприятиях широко применяется котельные установки, технологические печи, сушилки и другое оборудование, работающее на природном и сжиженном газе. Эти печи и оборудование, газопроводы и установки, регулирующие подачу газа, относятся к объектам повышенной опасности.
Природный газ, состоящий в основном (85-98%) из метана, взрывоопасен при концентрации в воздухе 4,5-17% по объему. Сжиженный газ представляет собой смесь пропана и бутана, взрывающуюся при концентрации в воздухе 2-10% по объему. Природный газ легче воздуха и при утечках может скапливаться в верхних частях помещения, а сжиженный газ, который почти в 2 раза тяжелее воздуха, - в нижних частях помещения, создавая в них взрывоопасную атмосферу.
Прокладываемые по территории предприятия и в помещениях газопроводы и располагаемые газорегуляторные установки, находятся под давлением до 0,6 МПа. Поэтому их эксплуатация осуществляется в соответствии с Правилами промышленной безопасности в области газоснабжения в Республике Беларусь, утвержденных Постановлением МЧС РБ от 02.02. 2009 г. №6. Правила содержат требования безопасности к устройству газопроводов внутри помещения, к потребляющему газ технологическому и производственному оборудованию, порядок приемки объектов в эксплуатацию, их обслуживания и надзора за ними.
Проектирование, строительство и эксплуатация газопроводов и использующего газовое топливо оборудования могут осуществлять инженерно-технические работники (ИТР) и рабочие, прошедшие обучение и сдавшие экзамены комиссии, в составе которой обязательно присутствует газотехнический инспектор местного органа Госпромнадзора. ИТР 1 раз в 3 года проходят периодическую проверку знаний Правил промышленной безопасности в области газоснабжения Республики Беларусь. На предприятиях, использующих газ в качестве топлива, из ИТР приказом назначаются лица, ответственные за безопасную эксплуатацию газового хозяйства, а для обеспечения надзора за его техническим состоянием создается газовая служба.
Привлекаемые к строительству и обслуживанию на предприятии объектов газового хозяйства рабочие ежегодно проходят повторную проверку знаний обслуживания и безопасной эксплуатации.
К самостоятельному выполнению работ по монтажу, наладке, ремонту, испытанию и эксплуатации газопроводов и газового оборудования (технических устройств), приборов, систем контроля и управления, газоиспользующих установок, средств защиты газопроводов от электрохимической коррозии допускаются рабочие, достигшие 18 лет и не имеющие медицинских противопоказаний, прошедшие обучение в специализированных учреждениях образования, проверку знаний и инструктаж по вопросам охраны труда и настоящих Правил в соответствии с Инструкцией по обучению в объеме выполняемых ими работ.
Правила по газовому хозяйству запрещают прокладывать газопроводы через подвальные помещения, склады и помещения взрывоопасных производств, помещения горючих материалов, электроподстанций, вентиляционных камер, а также в помещениях с коррозийноопасной средой. Газопроводы прокладываются с уклоном не менее 0,003 и на них должны устанавливаться устройства для спуска конденсата. Газопроводы внутри цеха оснащаются продувочными свечами с запорной арматурой, а на каждом отводе к оборудованию устанавливаются отключающие устройства.
После монтажа газопроводы и другие газовые объекты принимаются комиссией, в которую входят представители заказчика, строительно-монтажной организации, предприятия газового хозяйства и местного органа Госпромнадзора. Приемка объектов оформляется актом, который является документов, разрешающим их ввод в эксплуатацию.
Перед заполнением газом газопроводы проверяются контрольной опрессовкой давлением 10 кПа. Газ в цехи и к оборудованию подается газовой службой предприятия, а при ее отсутствии – предприятием газового хозяйства района.
Технологические печи и другие агрегаты, потребляющие газовое топливо, для обеспечения безопасной эксплуатации оснащаются приборами для измерения давления газа у горелок, воздуха в воздухопроводе грелок, разрежения в топке или в дымоходе до шибера; автоматическими устройствами для отключения подачи газа к горелкам при снижении давления воздуха в воздухопроводе у горелок, а также при остановке дымососа или снижении тяги в дымоходе; взрывными клапанами. Особые меры безопасности должны соблюдаться операторами технологических печей, работающих на газовом топливе, при их растопке. Топка и газоходы перед растопкой должны в течение 10-15 мин вентилироваться для удаления из них взрывоопасных газов. Из газопровода должен быть удален воздух путем продувки через продувочную свечу. После этого можно приступить к зажиганию газовых горелок, соблюдая установленный должностной инструкцией порядок этой операции и меры безопасности.
Контрольные вопросы
1. Какие требования безопасности предъявляются при проектировании, изготовлении и эксплуатации сосудов, работающих под давлением?
2. В чем заключается техническое освидетельствование сосудов, работающих под давлением?
3. Как обеспечивается безопасность эксплуатации баллонов со сжиженными, сжатыми и растворенными газами?
4. Какие требования безопасности должны соблюдаться при хранении и транспортировании баллонов?
5. В чем заключается особенность заполнения баллонов ацетиленом?
6. Какие меры безопасности установлены при перевозке сжиженных газов в цистернах и бочках?
7. Кто допускается к самостоятельному выполнению работ по монтажу, наладке, ремонту и эксплуатации газового оборудования?
8. Какие специальные требования предъявляются к проведению монтажа и сварочных работ на трубопроводах, подлежащих регистрации в органах Госпромнадзора?
9. Кто из рабочих и ИТР может быть допущен к эксплуатации оборудования, использующего газовое топливо?